Are You Getting the Most Out of Your Spiral Wound Membrane Elements?
Spiral wound membrane elements are a costly part of a dairy cheese and whey operation, if not maintained and cared for properly, a membrane investment could be a gateway for operational issues.
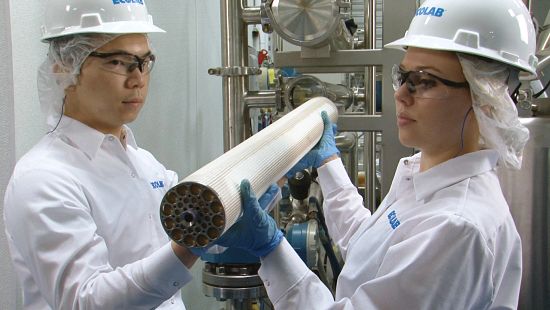
Spiral wound membrane elements are a costly part of a dairy cheese and whey operation, if not maintained and cared for properly, a membrane investment could be a gateway for operational issues. Membrane applications in these facilities may include reverse osmosis (RO), nanofiltration (NF), ultrafiltration (UF), and microfiltration (MF) or a combination of these to achieve the desired end product. Complex feed streams can include whole milk, skim milk, sweet whey, acid whey, UF permeate, UF concentrate, and others. The systems are typically cleaned daily using a clean-in-place (CIP) procedure that is specific to the application and soils encountered. At times, these membrane systems may experience a decline in performance, such as high production pressures, reduced production flux rates, reduced clean water flux rates, low protein and/or salt rejection, or shortened membrane life. These are often complex issues to resolve in order to get the most out of your membrane systems.
Membrane Root Cause Analysis
If your membranes are not performing as expected, you should consider a basic 3-step root cause analysis:
- What are the issues?
- How did these issues occur?
- Initiate actions to resolve and eliminate.
To identify issues and determine how they occurred, a thorough assessment of the overall membrane process should include a review of the upstream unit operations as well as the membrane system itself. Consider upstream systems like the cheese milk membrane system, cheese-make process and the whey processes including storage silos, separator, clarifier, pasteurizer, fines saver, etc.
As you assess these systems, ask questions like:
- Are these units operating properly?
- Is the separator bypassed on occasion causing higher fat levels to reach the membrane system?
- Are there any changes to the feed stream that could impact membrane performance (pH, storage time, addition of defoamer, process aid, change in cheese making process)?
Any issues or changes upstream can have a negative impact on the membrane system. Once you clearly identify what the problems are, you can begin investigating why and how these issues occurred and how to address them. You should next review the membrane system and its associated elements. Some key steps include:
Analyze water used for CIP, rinsing, and diafiltration. Water can be high in silica, iron, manganese, and total dissolved solids (TDS). These minerals can cause fouling issues and membrane damage if not in proper range.
Check your production parameters including pressure gauges, flow meters, and sensors to ensure they are working properly. Review baseline and stage pressures to determine if the system hydraulics are in the proper range to achieve ideal crossflow across membrane elements. Parameter checks will determine if you are achieving throughput as designed and maintaining product quality.
Ensure CIP procedures and checks are in order. Maintain proper chemistry throughout wash cycles by measuring pH and performing titrations; ensure you are not exceeding membrane element pH, chemical concentration, and temperature limits. Additionally, verify that your system hydraulics are in proper range for CIP and that rinsing between wash steps is optimized to minimize chemical carryover.
Review membrane elements for age and functionality such as protein and/or salt rejection and conduct an on-site autopsy of the membrane to diagnose for soil, telescoping, blisters, and any other defects that may impact performance.
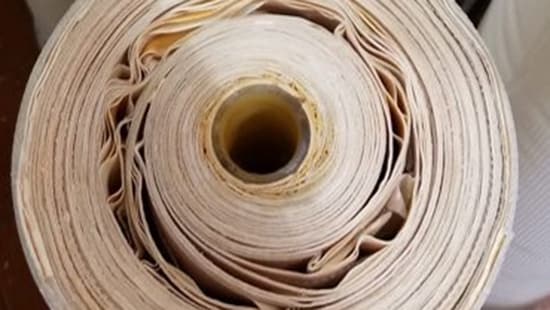
Spiral Wound Membrane Element with Severe Channeling
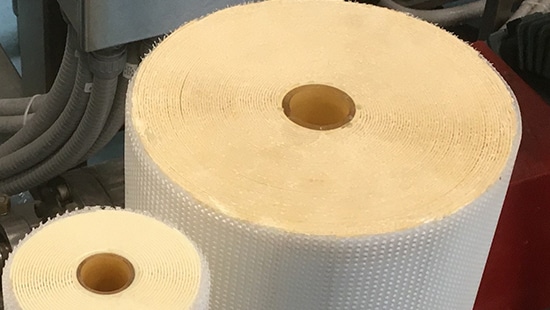
Spiral Wound Membrane Element in Good Condition
Go the Extra Mile
More thorough autopsies can be conducted by sending a membrane element to a laboratory with membrane specific diagnostic and performance testing capabilities. For soil scraped from the membrane surface, Fourier-transform Infrared Spectroscopy (FTIR), Energy Dispersive Spectroscopy (EDS), and ashing of the soil can determine the percent organic and percent inorganic as well as determine the constituents of the soil. In some cases, soils are not found on the membrane surface and cannot be physically removed for analysis. In this situation, a series of water and solvent extractions of a section of the membrane sheet can be undertaken to determine if there is soil in the membrane pores. The extraction followed up by the previously described analyses can help determine the extent and nature of pore fouling. Microbiological swabbing of the membrane sheet can confirm the sanitary nature of the element and if changes to the process need to be considered. Scanning Electron Microscopy (SEM) images and light microscopy can visually identify surface defects and/or soils at high magnification. The proper use of analytics for soil identification is often key to choosing the proper CIP products and processes if issues arise.
The laboratory that conducts the membrane autopsy should also be capable of running additional dynamic tests on the membrane elements or sheets. Additional dynamic tests include:
- Clean water flux under standard conditions with a flat sheet of the membrane in question is a good starting point to baseline the current condition of the membrane.
- Membrane integrity/rejection tests can be performed depending upon the type of membrane. RO membranes use sodium chloride as the test component, NF membranes use magnesium chloride, and UF and MFs can be tested against various proteins.
- Dye permeability testing can be effective in determining the integrity of a RO membrane and can provide clues to the mode of failure such as chemical degradation, punctures, or abrasion from feed stream particulates.
- The Fujiwara test can be used on RO membranes to provide insight into halogen oxidation damage to the membrane.
- Finally, full cleaning tests can be performed either on sections of flat membrane sheets or on the full element itself to determine if cleaning processes can improve the performance.
Membranes are a high value unit of operation, so membrane autopsies provide valuable insights that can be used to understand the root cause of performance issues. Understanding why performance issues are occurring enable dairy processors to optimize their operations while improving productivity, product quality, membrane life and profitability.