Precision Dispensing System for Membranes - Cheese Processing

The Precision Dispensing System for Membranes helped a cheese and whey processing plant in the Midwest improve productivity and worker safety.
Background
A cheese and whey processing plant in the Midwest was manually dispensing clean-in-place (CIP) chemistry to the brine and whey ultra-filtered (UF) membrane balance tanks in their plant.
Manual dispensing of chemistry often resulted in:
- Increased risk to chemical exposure for employees
- Inaccurate and inconsistent dispensing of chemistry
- Increased faulty washes from human error

Operators frequently experienced splashing when dumping the chemistry and it was also not uncommon to see open chemical drums in the production area posing not only safety concerns but the possibility of cross contamination.
Inaccurate and inconsistent dispensing of chemistry shocks the membranes, causing the membranes to be outside the parameters of the pH and ultimately deteriorating the life of the membrane over time.
Additionally, the plant experienced several instances of bad washes, requiring the plant to reclean the membrane, costing the plant 7 hours a year in production time equating
to $7,000.
The plant was looking for a safer and more efficient way to dispense CIP chemistry to their membrane systems and turned to Ecolab
for help.
The system eliminated chemical exposure for employees during dispensing and resulted in no additional rewashes of any membrane units.
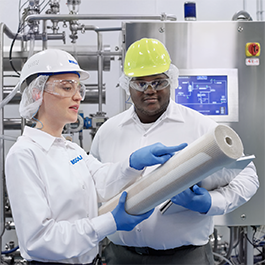
Solution
To help achieve the customers goals, Ecolab recommended the Precision Dispensing System for Membranes.
The Precision Dispensing System for Membranes is a flow-based membrane chemical dispensing system that accurately and safely dispenses cleaning chemicals and provides visibility into chemical consumption. Additional benefits include:
- Reducing improper chemical handling.
- Eliminating incorrect dispenses.
- Minimizing noncompatible chemical interactions.
The Precision Dispensing System for membranes also helps to potentially improve membrane life, by ensuring cleaning solution pH ranges do not exceed manufacturers recommendations, and decreases CIP time, by reaching target CIP parameters sooner.
The flow-based system offers separate modules for the acid, alkaline, surfactant and chlorine chemistries and has separate delivery paths for each membrane system. It utilizes volume-based dosing within 20 milliliters of targeted usage rates and can dispense chemicals for up to 5 membrane systems.
Additional features include the ability to configure recipes by volume and sequencing to each identified system, as well as out-of-spec alarms, consumption reports and optional PLC integration.
Results
The plant installed the Precision Dispensing System for Membranes and saw improvements in worker safety, productivity, and asset protection. The system eliminated chemical exposure for employees during dispensing and resulted in no additional rewashes of any membrane units. Moreover, it removed risk of shocking the membranes through consistent dosing, enabling the membranes to remain within the correct pH range and improving efficiency. Overall, the plant was able to save 132 hours a year in operator time that could be reallocated to other projects such as preventative maintenance and repairs. This plant is also happy with the aesthetics of the dispenser due to the fact that it is not prone to rusting.
Additionally, all the chemical drums can now be stored in a single isolated area out of the production area and next to the dispenser, making it easier to do inventory, maintain chemistry levels and eliminating safety concerns and cross contamination.
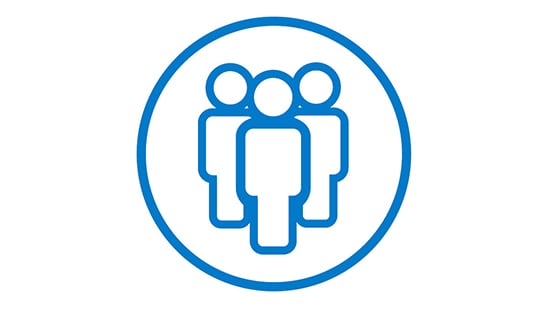
WORKER SAFETY
Eliminated operator exposure to chemistry. No longer have open chemical drums in production area.
Savings:
$10,000
per loss time accident
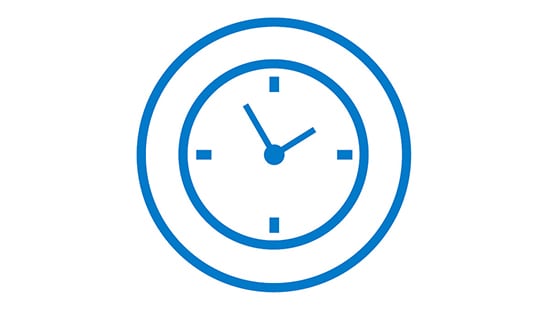
PRODUCTIVITY
Increased Productivity:
7
hours per year with elimination of rewash
$7,000per year
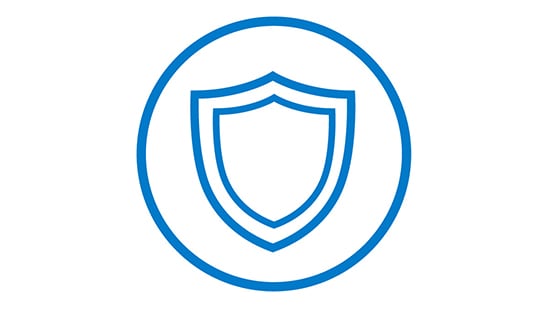
ASSETS
Saved Operator Time:
132
hours per year
Savings:
$2,600
Eliminated shocking the membranes when adding the chemical allowing them to stay within their pH ranges and improving membrane efficiency.
Total Value Delivered
$19,600 ANNUALLY