Precision Dispensing System for Membranes Milk Plant

The Precision Dispensing System for Membranes helped a milk plant improve productivity.
Background
A Midwest manufacturer of milk products was facing challenges with dispensing cleaning chemicals to their membrane systems. They were using a semi-automated dispensing system which pumped chemistry using time-based dispenses.
This posed many challenges including:
- No verification that the correct amount of chemistry was delivered to the membrane system.
- Chemical drums would run empty without any notification to the operator resulting in inefficient cleaning, causing the membrane unit to foul out quickly during production.
- Inconsistent run times for every wash.
- Increased cost and time from having to complete extra washes.
- Leaks in chemical lines would go unnoticed leading to:
- Potential workers safety issues from chemical overspray
- Severe damage to walls and floor around the dispensing equipment
The manufacturer wanted to improve the consistency of their washes in order to increase production and minimize downtime. Additionally, they were looking for a solution that would verify the correct amount of chemistry delivered to each membrane unit as per wash program designed for that system.
“I feel safer when I walk into the chemical supply area.”
—Membrane Operator
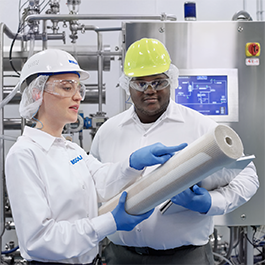
Solution
To help achieve the customers goals, Ecolab recommended the Precision Dispensing System for Membranes.
The Precision Dispensing System for Membranes is a flow-based membrane chemical dispensing system that accurately and safely dispenses cleaning chemicals and provides visibility into chemical consumption. Additional benefits include:
- Reducing improper chemical handling.
- Eliminating incorrect dispenses.
- Minimizing noncompatible chemical interactions.
The Precision Dispensing System for membranes also helps to potentially improve membrane life, by ensuring cleaning solution pH ranges (once appropriate wash recipe is configured into the systems) do not exceed manufacturer recommendations, and decreases CIP time, by reaching target CIP parameters sooner.
The flow-based system offers separate modules for the acid, alkaline, surfactant and chlorine chemistries and has separate delivery paths for each membrane system. It utilizes volume-based dosing within 20 milliliters of targeted usage rates and can dispense chemicals for up to 5 membrane systems.
Additional features include the ability to configure recipes by volume and sequencing to each identified system, as well as out-of-spec alarms, consumption reports and optional PLC integration.
Results
The installation of the Precision Dispensing System helped increase visibility into the customer’s chemical dispensing practices. After the installation of the system, the customer is fully confident that correct amount of chemistry is delivered to the correct membrane system every time. If issues such as an empty drum or leak arises, the operator receives notification alerting them to take immediate action to correct the problem. Consistent cleaning has led to improved production efficiencies eliminating the membranes from getting fouled quickly. As the system was able to dispense required chemical volumes accurately, cleaning process became more reliable and uniform thereby leading to consistency of production (duration, throughput) after every single wash. The manufacturer was able to eliminate 1 wash per week on their UF1 system, increasing production by 8 hours per week and $25,000 in annual chemical savings. Additionally, they were able to reduce their chemical consumption of Ultrasil 09 from 18 gallons per wash to 9 gallons due to the unit cleaning better thereby saving $31,000/per year. They also eliminated all safety concerns from potential chemical exposure.
Conclusion
The Precision Dispensing System for membranes helped increase productivity, improve workers safety and save in overall cost.
“The unit has really exceeded my expectations.”
— Customer Management
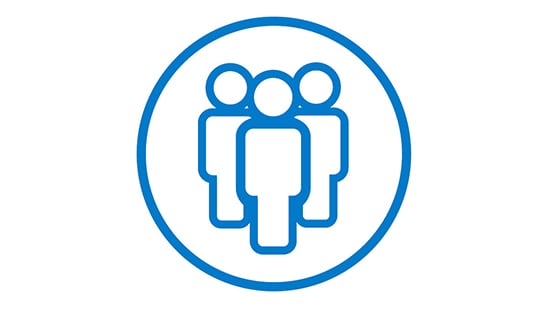
WORKER SAFETY
Chemical leaks no longer go undetected
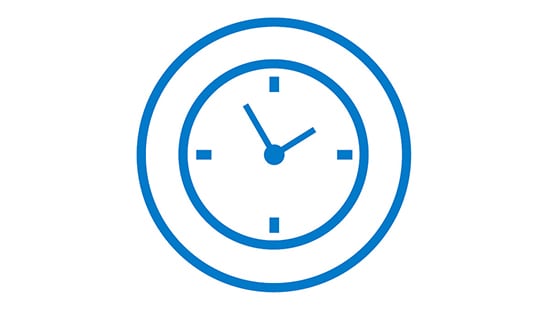
PRODUCTIVITY
Increased Productivity:
8
hours per week with elimination of 1 entire wash/week
Contributed to:
$3.9M
in additional revenue
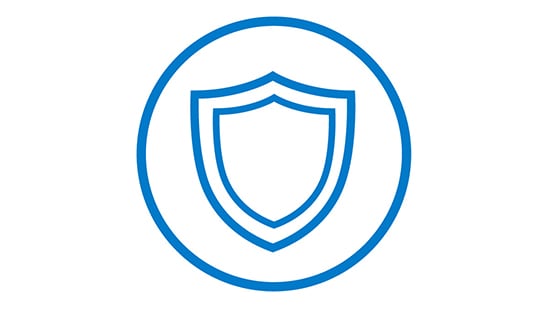
ASSETS
Reduced Chemicals:
$25,092
Reduced Washes:
$31,200
Reduced Ultrasil™ 09 by 9 gal/wash
Eliminated damage to walls and floors due to chemical leaks:
$7,500
Total Value Delivered
$4M ANNUALLY